Common name 2507, 2507, duplex steel, high molybdenum duplex steel, duplex steel 2507 duplex steel
Standards UNS S32750, DIN/EN 1.4410, ASTM A240, ASME SA-240
Main ingredients 25Cr-7Ni-4Mo-0.27N
Duplex Steel 2507 (UNS S32750) alloy consists of 25% chromium, 4% molybdenum and 7% nickel. It has strong strength and corrosion resistance and is mainly used in chemical processing, petrochemical industry and subsea equipment. It has strong resistance to chloride corrosion, high thermal conductivity and low thermal expansion coefficient. The higher chromium, molybdenum and nitrogen content makes it highly resistant to pitting corrosion, crevice corrosion and uniform corrosion.
-------------------------------------------------- ----------------------------------
Duplex Steel 2507 (UNS S32750)
25% chromium duplex stainless steel
General properties
Duplex steel 2507 is a high-molybdenum duplex stainless steel composed of 25% chromium, 4% molybdenum and 7% nickel. It has strong strength and corrosion resistance and is mainly used in chemical processing, petrochemical industry and subsea equipment. It has strong resistance to chloride corrosion, high thermal conductivity and low thermal expansion coefficient. The higher chromium, molybdenum and nickel content makes it highly resistant to pitting corrosion, crevice corrosion and uniform corrosion.
Its impact strength is also very high. Duplex steel 2507 is not suitable for use in temperatures above 570°F. Its toughness will decrease if it is exposed to such an environment for a long time.
-------------------------------------------------- ----------------------------------
Application areas
Oil and gas industry equipment
Offshore platforms, heat exchangers, underwater equipment, firefighting equipment
Chemical processing industry, vessel and pipe industry
Desalination plants, high-pressure RO plants and submarine pipelines
Mechanical components (high-strength, corrosion-resistant components)
Energy industry FGD system, industrial scrubbing system, absorption tower
-------------------------------------------------- ----------------------------------
standard
ASTM/ASME..........A240 - UNS S32750
EURONORM............ 1.4410 - X2 Cr Ni MoN 25.7.4
AFNOR............Z3 CN 25.06 Az
-------------------------------------------------- ----------------------------------
Corrosion resistance
uniform corrosion
The high chromium and molybdenum content of duplex steel 2507 makes it highly resistant to overall corrosion against organic acids such as formic acid and acetic acid. Duplex steel 2507 alloy also has strong corrosion resistance to inorganic acids, especially those containing chlorides.
Compared with 904L, duplex steel 2507 has stronger corrosion resistance against dilute sulfuric acid mixed with chloride ions. 904L is an alloy in the austenitic state, specifically designed to resist pure sulfuric acid corrosion.
Grade 316L cannot be used in hydrochloric acid environments as it may suffer from local or overall corrosion. Duplex steel 2507 can be used in dilute hydrochloric acid environments and has strong resistance to pitting corrosion and crevice corrosion.
intergranular corrosion
The lower carbon content of Duplex Steel 2507 greatly reduces the risk of carbide precipitation between the grains during heat treatment. Therefore, this alloy has a strong ability to resist carbide-related intergranular corrosion.
stress corrosion cracking
The dual-phase structure of duplex steel 2507 makes it highly resistant to stress corrosion cracking. Due to its higher alloy content, duplex steel 2507 has better corrosion resistance and strength than 2205. Duplex steel 2507 is particularly suitable for offshore oil and gas extraction equipment. Pitting corrosion
There are many methods to test the pitting corrosion resistance of steel products in solutions containing chloride. The above data are based on the electrochemical technology mentioned in ASTM G61. The critical temperature of pitting corrosion of high-performance stainless steel in 1M sodium chloride solution is specified. The experimental results demonstrate the superior resistance to pitting corrosion of duplex steel 2507. Test data for each level is represented by a dark gray color.
crevice corrosion
Cracks are almost inevitable in construction and other aspects, which makes stainless steel more susceptible to corrosion in chloride environments. Duplex steel 2507 has strong resistance to crack corrosion. The critical temperature for crack corrosion resistance of duplex steel 2507 and other high performance stainless steel products is shown in the figure above.
The iso-corrosion curve in sulfuric acid containing 2000 ppm chloride ions is 0.1 mm/year. The iso-corrosion curve in hydrochloric acid is 0.1 mm/year. The dashed line represents the boiling point. Critical corrosion temperature of various alloys in 1m NACI Critical crevice corrosion temperature of various alloys in 10% FeCl3
-------------------------------------------------- ----------------------------------
chemical composition
Average (weight %)
C Cr Ni Mo N Others
0.020 25 7 4.0 .27 S=0.001
PREN = [Cr%] + 3.3 [Mo%] + 16 [N%] ≥ 40
-------------------------------------------------- ----------------------------------
Mechanical behavior
Mechanical and physical properties
Duplex steel 2507 has high tensile strength, impact strength, low thermal expansion coefficient and high thermal conductivity. These properties apply to many structural parts and mechanical components. The mechanical properties of duplex steel 2507 at lower and higher temperatures are shown in the figure below. All experimental data are obtained from testing samples after annealing and quenching treatment.
Duplex Steel 2507 should not be exposed to temperatures above 570°F for long periods of time as this may weaken its toughness. The data in the following tables only apply to forged products and should not be regarded as maximum or minimum values unless otherwise stated.
-------------------------------------------------- ----------------------------------
processing
thermoforming
Duplex Steel 2507 should be hot formed within the temperature range of 1875°F-2250°F, immediately thereafter solution annealed at a temperature not less than 1925°F, and then rapidly water quenched.
cold forming
Many common stainless steel forming methods are suitable for duplex steel 2507. This alloy has higher yield strength and lower ductility than austenitic grades of stainless steel. Therefore, processors believe that it is necessary to enhance the forming strength, increase the bending radius, and also consider the rebound factor. Compared with austenitic grades, the drawing and stretch forming processes of 2507 are more difficult to operate. When forming requires 10% or more cold deformation, we recommend solution annealing and quenching.
heat treatment
Duplex steel 2507 should be solution annealed and quenched after hot forming or cold forming. The solution annealing temperature should not be lower than 1925°F and should be immediately followed by air or water quenching. In order to obtain the ideal corrosion resistance, the heat-treated products must also be pickled and rinsed.
-------------------------------------------------- ----------------------------------
welding
Duplex steel 2507 has good weldability and can be welded by: SMAW, GTAW, PAW, FCW, or SAW. When welding duplex steel 2507, it is recommended to use 2507/P100 metal, which will form a proper duplex structure .
It is not necessary to preheat Duplex 2507 unless you wish to prevent cold metal concentration. Intermediate welding temperatures should not exceed 300°F, otherwise the integrity of the weld will be compromised. Root application should be with argon or 90% N2/10 % H2 purification gas is shielded to ensure its strong corrosion resistance. The latter effect will be better.
If only one side is being welded, it is not possible to clean it after welding. We recommend using GTAW for the root pass. Without filler metal, GIAW and PAW cannot be performed unless it can be cleaned after welding. If the heat supply is 5-38 kJ/in. SMAW or GTAW should be used. If the heat supply is 50kJ/in., SAW should be used.
Mechanical properties Tensile strength: σb≥730Mpa
Elongation: δ≥15%
Material description: The main chemical components Cr, Ni, Mo, N, etc. are improved to a certain extent compared with 2205, 2304, and 2101. They have better performance in oxidation resistance, acid corrosion resistance, seawater corrosion resistance, chloride ion corrosion, etc., and at the same time Also has good strength.
Typical working conditions: 30% dilute sulfuric acid, below 60℃, annual corrosion rate <0.1mm
Application areas Pulp and paper industry, seawater desalination, flue gas purification, heat exchangers, chemical tanker piping systems, seawater systems, etc.
Matching welding consumables E2594
Supply form: plates, strips, bars, pipes (welded pipes and seamless pipes), wires, forgings, bare rods, flanges, welding materials
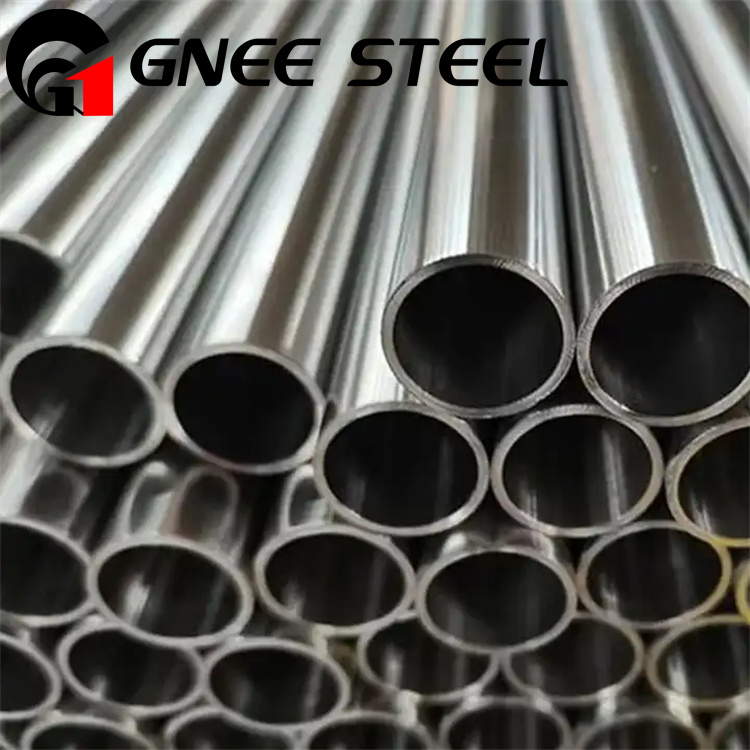
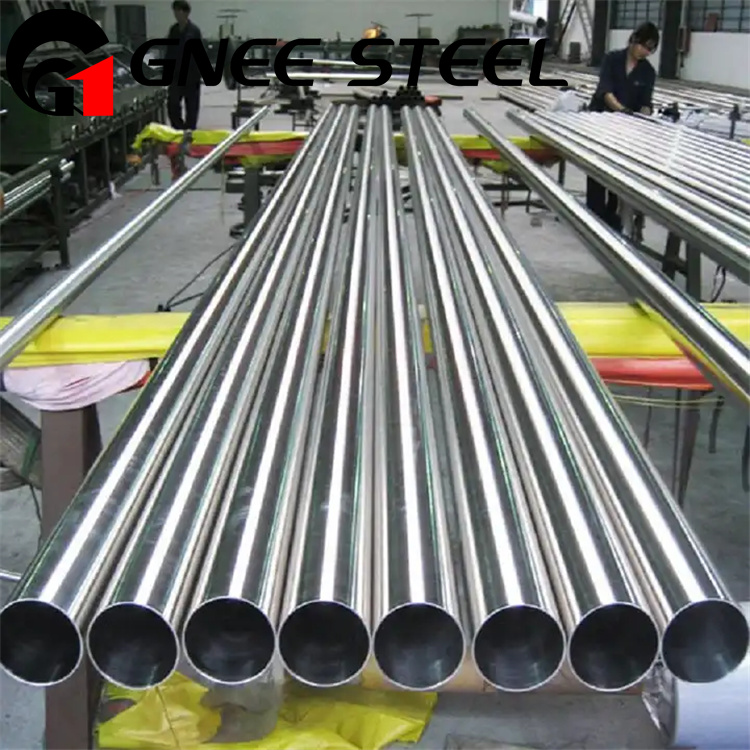